Epic Eye Pixel Welding
Safety Instructions
Safety Statement
-
Before using this product, please read the product manual and fully understand the relevant safety information. Failure to follow the instructions may result in equipment damage, serious injury, or death.
-
Transfer assumes no legal responsibility for any personal injury, property loss, or other accidents caused by non-compliance with this manual or improper operation of the product.
Precautions
-
Avoid using the camera in environments with dust, strong electromagnetic interference, direct sunlight, or outside the specified temperature and humidity range.
-
Do not stare directly into the projection beam while the camera is operating to avoid eye injury.
-
Ensure the camera window is clean. Use a lint-free cloth to clean the window if necessary.
-
Do not perform installation, disassembly, or cleaning while the camera is powered on.
-
During transportation and installation, avoid severe impact or dropping of the camera.
-
If any abnormal conditions occur (e.g., unusual sounds, odors, or smoke), immediately cut off the power and perform an inspection.
-
Do not modify the camera or its power cables.
Packing List
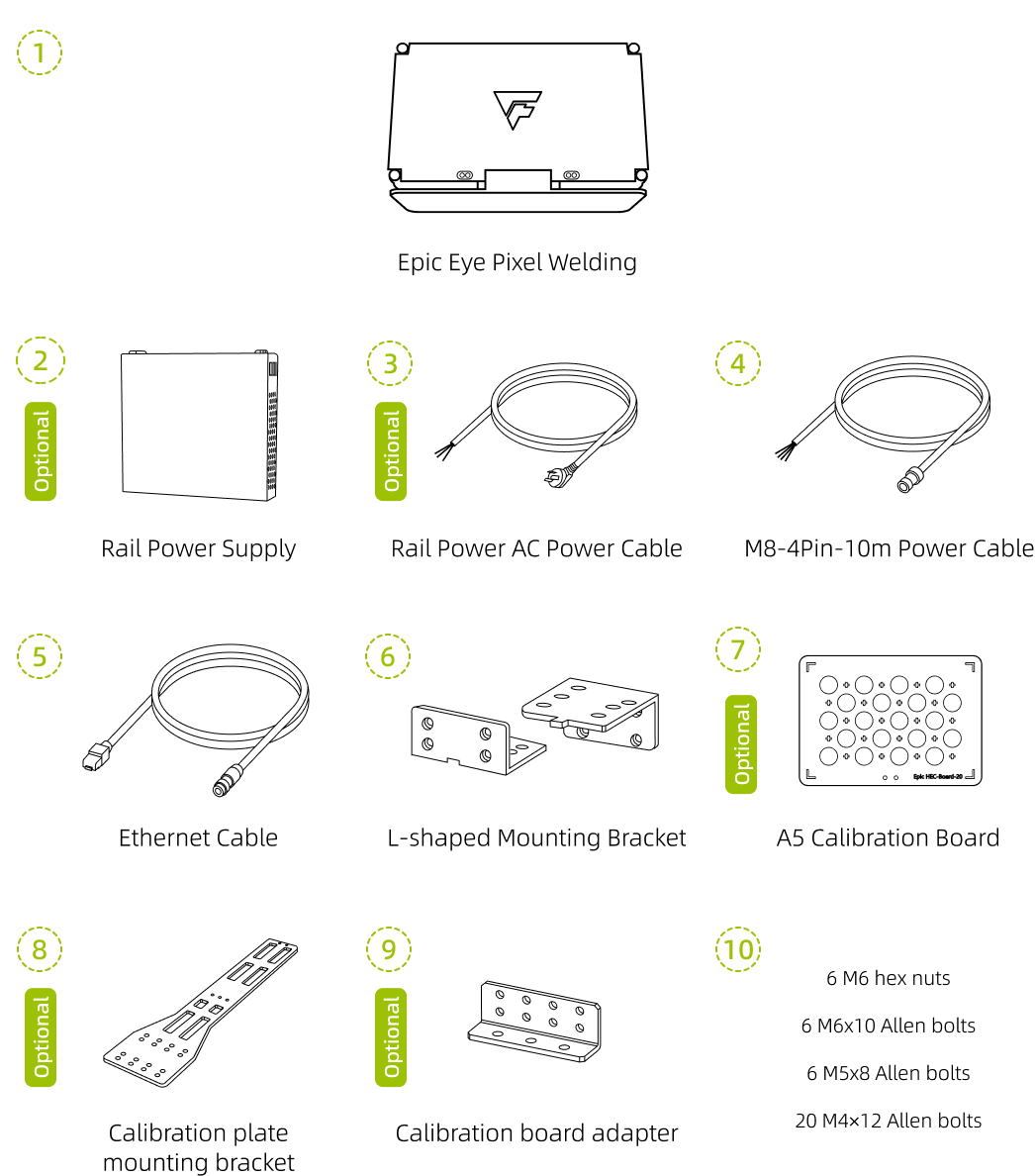
Upon unboxing, check the camera and its accessories for any damage, rust, or deformation, and verify the completeness of the items against the packing list. If any damage or discrepancies are found, please contact Transfer.
Technical Specifications
Technical Parameters
System Parameters |
Baseline Length |
85mm |
Recommended Working Distance |
300mm~700mm |
|
Optimal Working Distance |
500mm |
|
Near Field of View |
295mm×175mm@0.3m |
|
Far Field of View |
670mm×390mm@0.7m |
|
VDI/VDE Measurement Accuracy(1) |
0.1mm@0.5m |
|
Z-axis Single Point Repeatability |
0.03mm@0.5m |
|
Pixel Count |
2.3 million |
|
Resolution |
1920×1200 |
|
Typical Acquisition Time |
0.2s~0.7s |
|
Power Supply |
24V ⎓ 2.5A |
|
Peak Power |
32W |
|
Average Power Consumption |
4.5W |
|
Standby Power Consumption |
2.5W |
|
Hardware Parameters |
Dimensions(L*W*H) |
130mm×71mm×79mm |
Installation Method |
Fixed Installation/End-of-Arm Installation |
|
Communication Interface |
Gigabit Ethernet |
|
Light Source |
Blue LED(440nm) |
|
2D Camera |
Monochrome |
|
Environmental Parameters |
Operating Temperature Range |
0℃~50℃ |
Operating Humidity Range |
20%~90% RH No Condensation |
|
Protection Rating |
IP65 |
|
Cooling Method |
Passive |
|
Weight |
1.01kg |
|
Storage Temperature |
-20℃~70℃ |
|
Storage Humidity |
20%~90% RH No Condensation |
(1): Based on VDI/VDE 2634 Part II standard
Subject to change without notice!
Installation and Connection
Installing the Camera
Mounting Method 1:
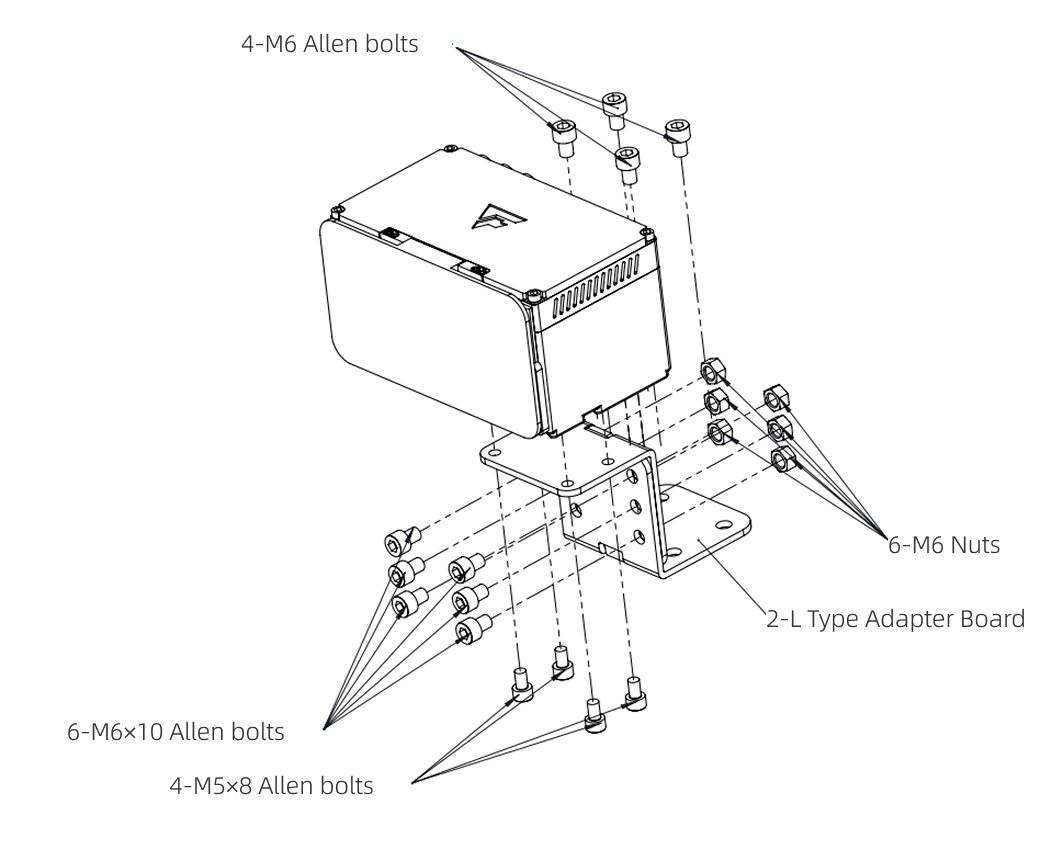
Mounting Method 2:
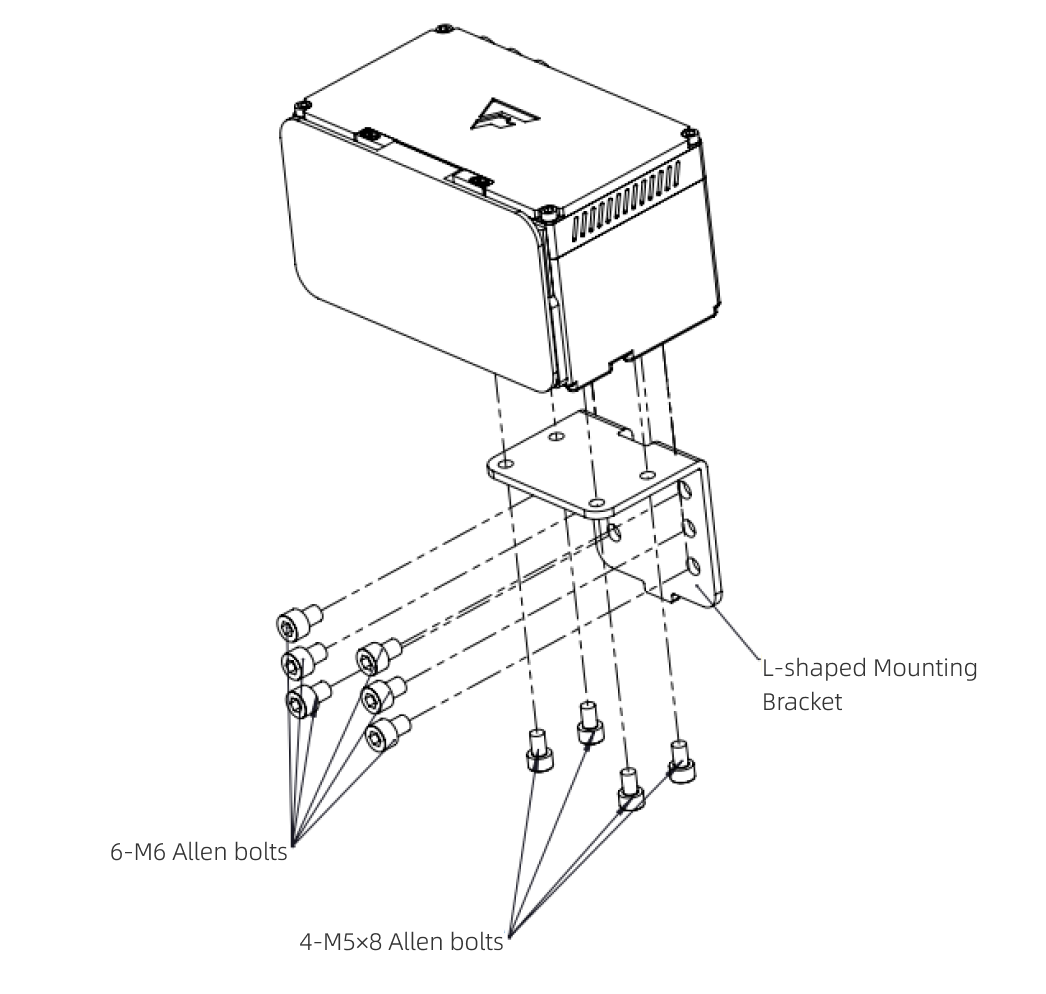
|
Mounting the Camera on the Bracket
Mounting Method 1:
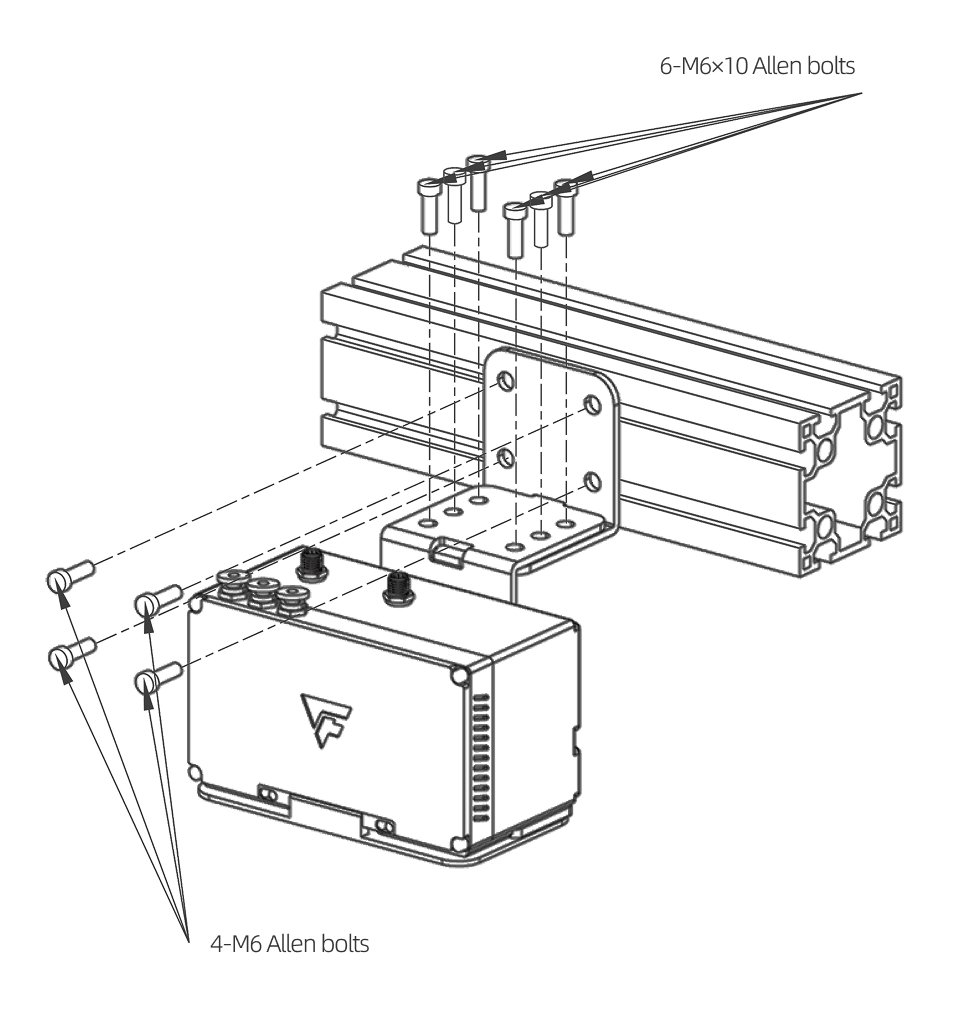
Mounting Method 2:
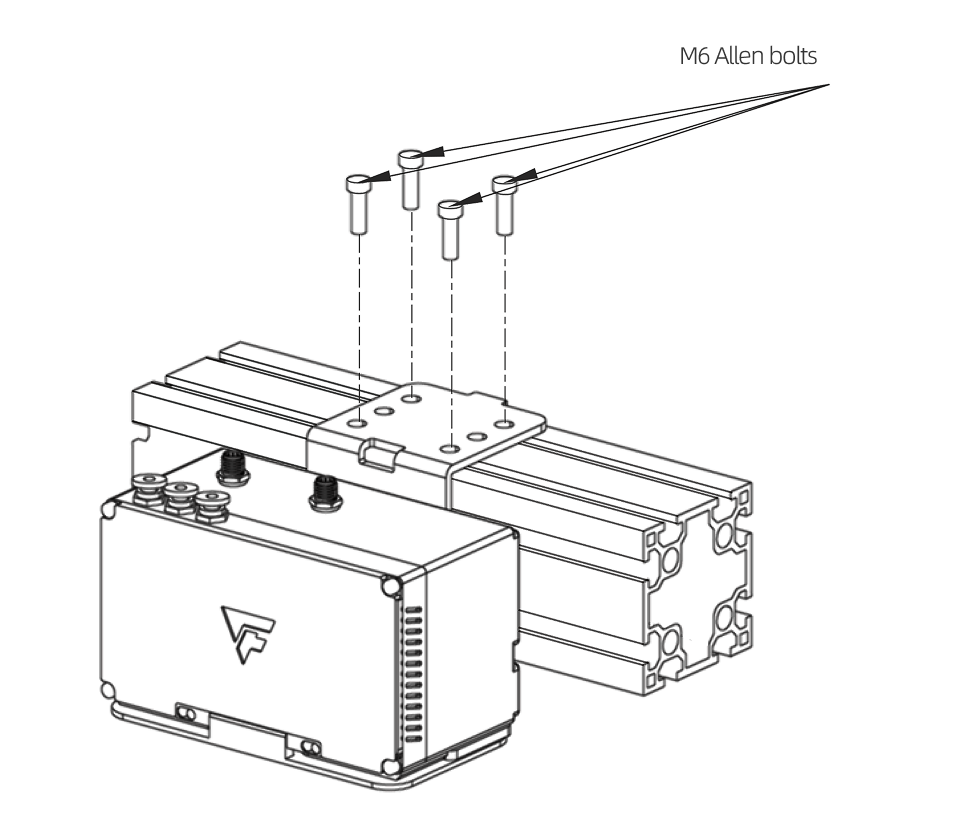
|
Cable Connections
Connection Guidelines
-
Do not plug or unplug cables while powered on. Connect all cables before turning on the power.
-
Align the plug with the socket and tighten slowly. Avoid excessive force.
-
Use cable ties to secure the camera network cable, power adapter, and power cord.
-
When connecting via a router, use the LAN port for all network cables.
-
For router or switch connections, use a gigabit router, switch, and dual-head RJ45 cable.
Wiring Connections
-
Camera Directly Connected to Industrial PC
-
Industrial PC; 2. Camera Ethernet Cable; 3. Camera; 4. M8-4Pin-10m DC Power Cable; 5. Rail Power Supply; 6. Robot
-
-
Camera Connected to Industrial PC via Switch
-
Industrial PC; 2. Ethernet Cable; 3. Switch; 4. Camera Ethernet Cable; 5. Camera; 6. M8-4Pin-10m DC Power Cable; 7. Rail Power Supply; 8. Robot
-
Power Cord Technical Specifications
Physical Parameters
Model |
Straight |
Angled |
CBL-PWR-8-10M CBL-PWR-8-20M CBL-PWR-8-30M |
CBL-PWR-8-20M-LU CBL-PWR-8-30M-LU |
|
Color |
Black |
|
Outer Sheath Material |
PVC |
|
Outer Diameter |
6.5(+0.15/-0.15)mm |
|
Connector |
M8, straight or angled, 4-pin loose wire end |
|
Conductor Diameter |
0.5 mm² |
|
Static Bending Radius |
65 mm |
|
Dynamic Bending Radius |
80 mm |
|
EMI shielding effectiveness |
Aluminum foil, metal woven mesh, double-layer shielding |
|
Safety |
RoHS Compliant Flame Rating: V-1 |
|
Cable Carrier Test |
Bending Radius: 65mm Stroke: 1000mm Speed: 3200 mm/s Cycles: ≥ 5 million |
|
Compatible Camera Models |
Pixel Welding, Pixel Pro, Pixel Mini |
Dimensions
Unit: mm

Model |
L |
---|---|
CBL-PWR-8-10M |
10m |
CBL-PWR-8-20M |
20m |
CBL-PWR-8-30M |
30m |
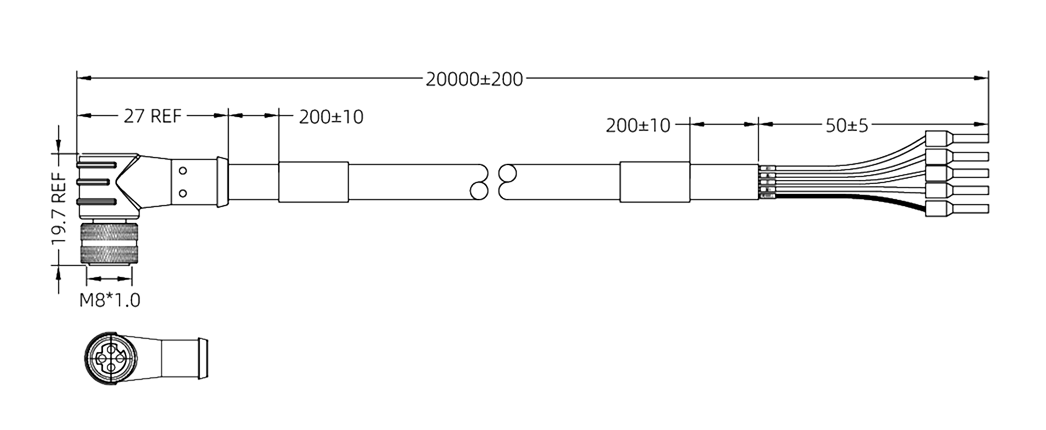
Model |
L |
---|---|
CBL-PWR-8-20M-LU |
20m |
CBL-PWR-8-30M-LU |
30m |
Ethernet Cable Technical Specifications
Physical Parameters
Model |
Straight Head |
Angled Head |
CBL-ETH-10M, CBL-ETH-20M, CBL-ETH-30M |
CBL-ETH-20M-LU |
|
Color |
Black |
|
Outer Sheath Material |
TPU |
|
Filler |
Cotton Yarn |
|
Outer Diameter |
5.9 (+0.1/-0.2) mm |
|
Connector |
M8, straight or angled, 4-pin Open End |
|
Conductor Diameter |
26 AWG |
|
Static Bending Radius |
60 mm |
|
Dynamic Bending Radius |
50 mm |
|
EMI shielding effectiveness |
Aluminum foil, metal woven mesh, double-layer shielding |
|
Safety |
RoHS Compliant Flame Resistance: V-1 |
|
Drag Chain Test |
Bending Radius: 50 mm Stroke: 1000 mm Speed: 3200 mm/s Cycles: ≥ 1 million |
|
Compatible Camera Models |
Pixel Welding, Pixel Pro, Pixel Mini |
Calibration Board Installation
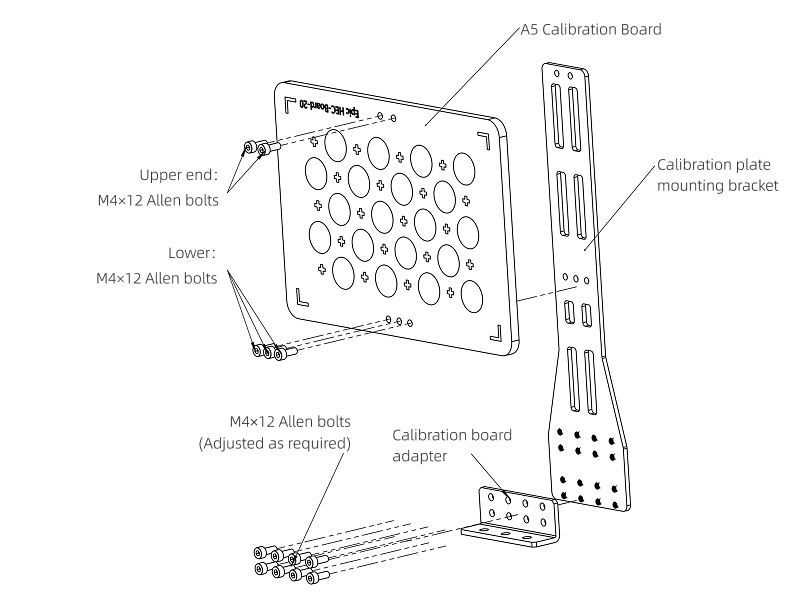
|
Maintenance and Care
Regular maintenance of industrial 3D camera hardware is crucial for ensuring stable operation and measurement accuracy. It not only extends equipment service life but also helps in timely detection and prevention of potential issues, reducing equipment failure rates and ensuring continuous stable operation of production lines. Please strictly follow the maintenance regulations and keep proper records.
Daily Inspection
-
Check power supply status regularly, inspect power cable connections for proper contact, ensure stable power voltage output meeting power supply specifications. When necessary, use UPS (Uninterruptible Power Supply) to prevent unexpected power outages.
-
Verify network connection stability and ensure network transmission rates meet requirements.
-
Monitor working environment temperature and humidity for compliance with specifications, ensure good ventilation for proper camera cooling.
-
Inspect camera housing integrity, ensure no damage, deformation, or corrosion, and avoid risks of scratching or collision with surrounding objects.
-
Check camera mounting and adapter fixtures for tightness, ensure no deformation, looseness, or wobbling.
-
Inspect cable connector stress conditions, ensure reasonable cable routing without excessive bending, and check cable sheathing for aging or cracking.
Regular Cleaning
Clean the camera regularly to ensure the lens is clean, free from visible dust and stains. Use a clean soft cloth to wipe the camera body, and clean the camera lens with a clean, soft, lint-free cloth dampened with lens cleaner or glass cleaner to avoid scratching the lens.
Cautions
-
Power off the equipment before cleaning.
-
Do not use alcohol or other corrosive cleaning agents.
Storage and Transportation
-
Use original packaging or professional shock-proof cases for camera storage and transportation.
-
Ensure storage environment temperature and humidity meet standards.
-
Avoid severe vibration and impact, keep away from strong magnetic fields.
-
Maintain correct placement orientation, avoid direct exposure of lens to strong light sources such as sunlight.
-
Conduct thorough cleaning before long-term storage, perform regular power-on checks (every 3 months).
Technical Support Channel
For technical support, please call the official hotline at 4000-191-161 and follow the voice prompts to press 3 to enter the technical support channel.
Legal and Compliance
Disclaimer
Transfer assumes no responsibility for accidents caused by non-compliance or unauthorized modifications.